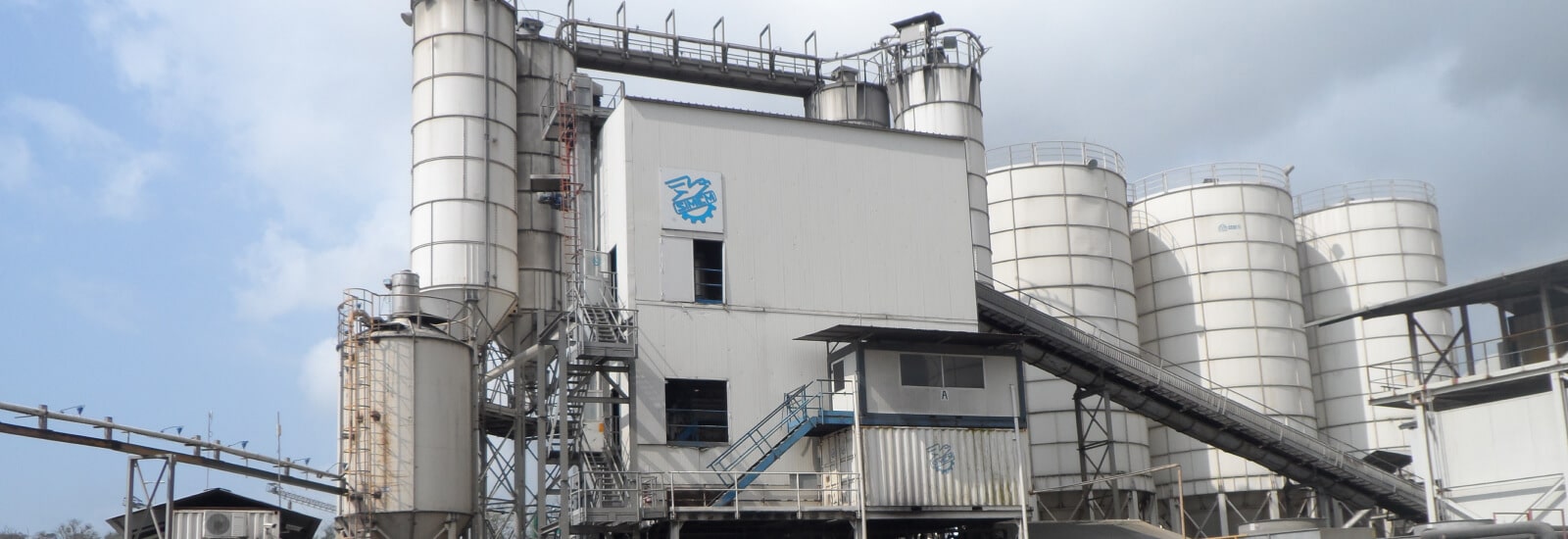
A Major Infrastructure Project
Panama recently oversaw an extensive construction project designed to expand the Panama Canal to give it the ability to handle “Post Panamax Vessels.” Simem
History
The concept of a canal near Panama dates to the early 16th century. The first attempt to construct a canal began in 1880 under French
The Challenge
A consortium named Grupo Unidos
The Solution
Many factors had to be taken into consideration for the design of these concrete plants. For instance, the raw material requirements, the output capacity, and the concrete placing temperature. In the end, the plant layout was based on a shared aggregate section serving two independent mixing towers, each containing two Simem MSO6000-HLS twin shaft mixers with an output capacity of 4.5 m3 of compacted concrete per batch. The combined capacity of the two mixer towers, with a total of 4 mixers, is 720 m3 per hour.
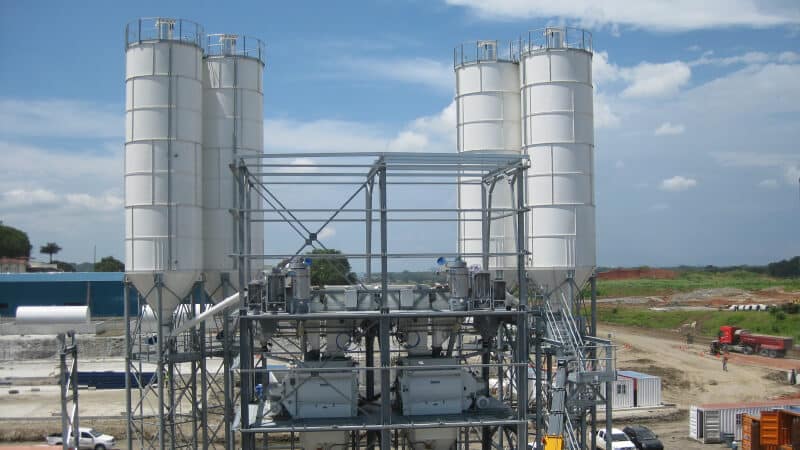
For the concrete production, five different types of aggregates were utilized, three fractions of stones and two fractions of sand. Due to the concrete placing temperature requirement of 10° C in an area with a typical ambient temperature of 35° C and higher, the complete system also contained a considerable cooling solution. To ensure the placing temperature was maintained, the aggregate was loaded into the bins on a demand system. The control system of the concrete plant sends continuous consumption information to the aggregate loading system, which loads the bins with the different aggregate fractions as required. The aggregate is cooled during the loading process into the aggregate bins, which have a total storage capacity of 750m3 with a capacity for each of the five fractions for one hour of production. The complete aggregate section is enclosed with insulated panels and cold air is then blown into this enclosure to control the temperature of the aggregate. Cold air is also blown directly into the aggregate bins for some of the material fractions.

State-of-the-art batching and mixing “super plants”, scaled and configured to meet any output capacity or application.
More About WetBetonIn order to keep up with the cycle time of 80 seconds, it was necessary to use one aggregate scale for each aggregate fraction. Five scales served mixing tower A and another five served mixing tower B.
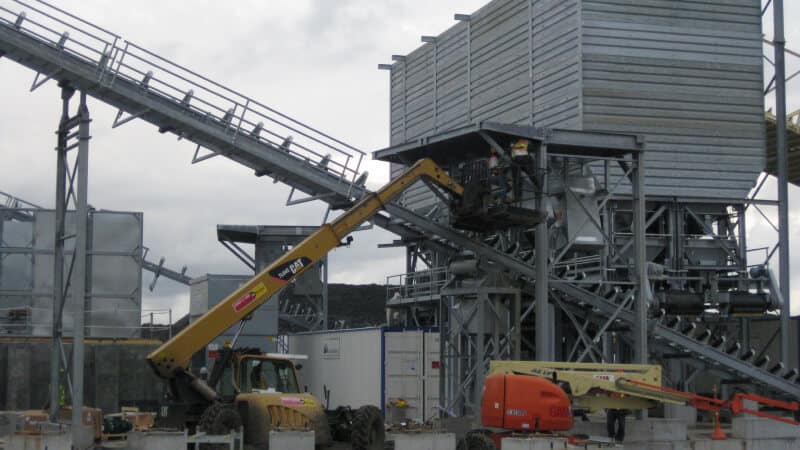
The aggregate is transported from the scales to the holding hopper above each mixer with a high capacity extraction belt and an inclined belt before passing a diverter chute into the selected holding hopper. The controls allow for the consecutive batches to be on the same belt conveyor spaced out by the use of timers and material sensors in order to give the diverter chute time to change between the holding hoppers. Each mixing tower is served by a double set of ice scales. The ice is discharged onto the inclined aggregate belt conveyor.
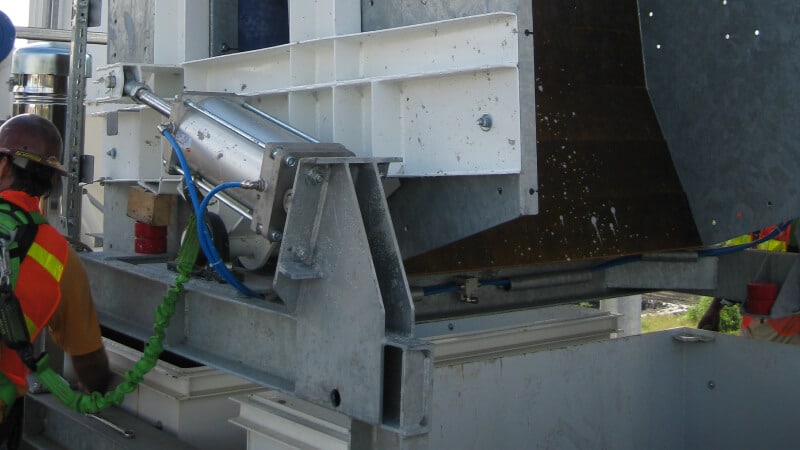
One type of cement and one type pozzolan
Water is also dosed by the use of scale, and the plants are ready for use of clean water (chilled) and slurry water. Slurry water was available from the BetonWash 25 concrete reclaimers supplied by Simem S.p.A. Three types of admixtures will be utilized and they are dosed with the use of 2 scale units. One unit with double chambers and the second one with a single chamber. Due to the different volumes of the admixtures, two units were supplied to ensure the required accuracy.
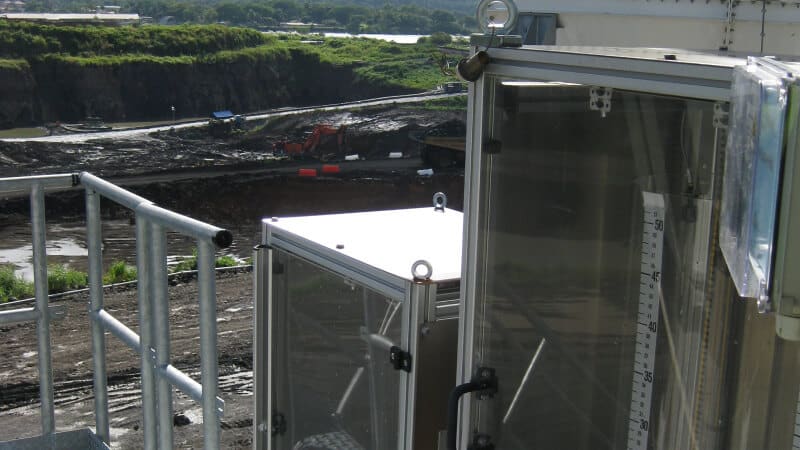
The MSO 6000-HLS
Most of the concrete produced was loaded into open bed agitator trucks with a capacity of 9 m3, making it necessary to double batch to fill the truck. In order to reach the required capacity, each mixer was equipped with a holding hopper able to hold one batch, thus ensuring that the truck movement would not delay the mixer discharge. The plant is also equipped with an automated moveable loading chute if traditional truck mixers are being used.
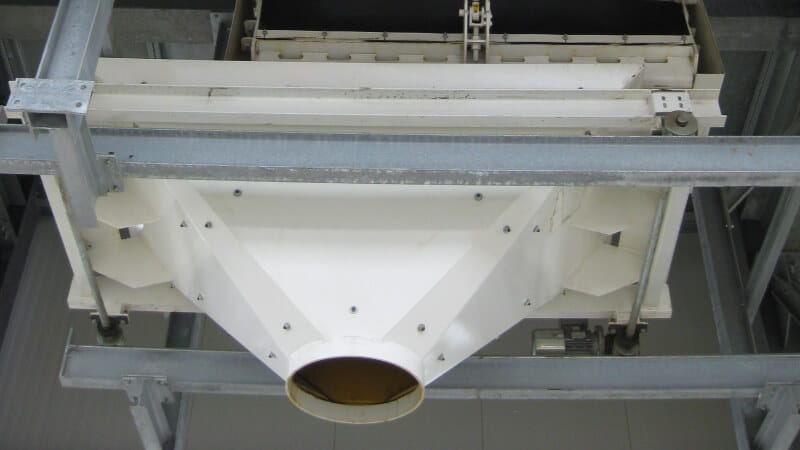
Design And Production
All equipment was designed and produced by Simem S.p.A. in Italy and shipped to the sites. Each mixing tower is considered a separate
The equipment has been installed under the supervision of personnel from SIMEM S.p.A.’s subsidiary in USA, Simem America Corp. The installation began at the end of June 2010 and the first batch of concrete was produced from plant “A” in Panama City, in mid-November of the same year. Starting in January/February 2011, regular production began with a gradual increase in volume until full capacity is reached and required in March/April of 2011. The full Panama Canal expansion project was opened on June 26, 2016.