Federico Furlani, CEO of SIMEM, interview with Ingenio, a leading industry publication in Italy
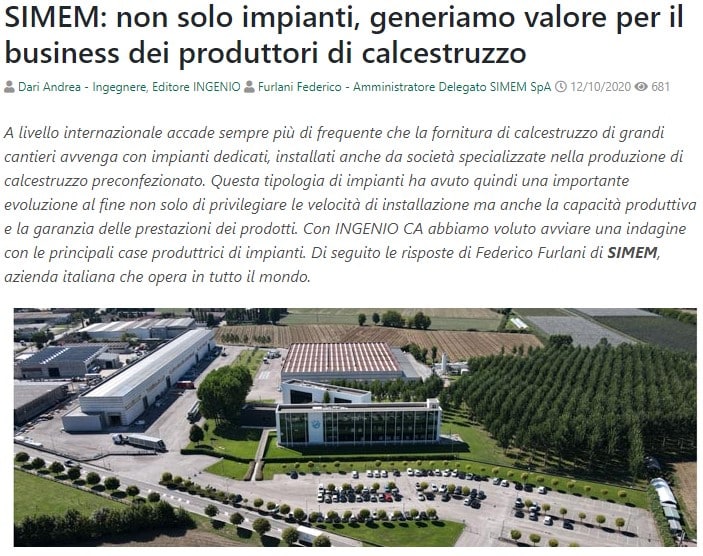
Original Publication: Ingenio
At international level it is increasingly the case that the supply of concrete from large construction sites takes place with dedicated plants, also installed by companies specialized in the production of pre-packaged concrete. This type of plant has therefore had an important evolution in order not only to give priority to installation speeds but also to production capacity and the guarantee of product performance. With INGENIO CA we wanted to launch an investigation with the main manufacturers of plants. Below are the answers of Federico Furlani of SIMEM, an Italian company that operates all over the world.
The evolution of mobile concrete production plants
- Investments in infrastructure have led to a worldwide increase in the presence of mobile installations in large construction sites. In the last 10 years has there been an evolution of mobile concrete production plants. If so, which one?
Federico Furlani:
Mobile systems respond to a logistical need to optimize the flow of materials, as well as quality of the production process that guarantees the characteristics of concrete at the time it is put in place.
The world concrete market, mainly oriented towards the use of (what in Italy we call) pre-draining, has seen an extraordinary increase in the adoption of mobile or transportable systems, to bring the packaging of concrete as close as possible to the work to be carried out, especially for those infrastructure projects far from fixed concrete plants.
The technological evolution of mobile systems has gone, and is continuing to go, in the direction of reducing transport and assembly times and costs on the one hand and guaranteeing production quality on the other.
Mobile concrete plants: the SIMEM range
2. What is your proposal for mobile systems? With what characteristics?
Federico Furlani:
SIMEM offers different ranges of mobile systems:
• EAGLE range: easy to transport and install, pre-assembled and pre-wired, designed for transport with standard trucks and/or containers, equipped with mixer and available to cover a production range from 70 to 180 mc/h;
• ZINGO range: semi-mobile dry production plants, therefore without mixer, have the same transportability characteristics as eagles, cover a production range from 40 to 100 mc/h;
• MMX: patented in 2010 is characterized by engineering peculiarities that make it unique. The complete mixing unit of weighing systems, retractable support structure and inerrti feeding belt, can be transported with only one vehicle. Same principle for the inerti group, with ramps and banks that close during the shipping phase becoming a single module. It guarantees productions up to 130 mc/h with a 3.33 mn rendered double axle mixer;
• BISON: super mobile system, does not require foundation works, and from arrival on site it becomes operational in a few hours. Born for the production of cemented mixtures, cold asphalt, inertizations and concrete, it combines the concept of mobility with production versatility. Equipped with a continuous double-axis mixer, it covers productions from 250 to 500 Ton/h.
Mobile concrete systems: some reference
3. Can you tell us some important reference?
Federico Furlani:
There are many references accumulated in the history of SIMEM, in particular some noteworthy projects that see the supply of mobile systems:
• 2 x EAGLE 5000 installed inside the Brenner Base Tunnel;
• 2 x EAGLE 7000 and 1 x EAGLE 5000 installed for the construction of Mexico City airport;
• 2 x EAGLE 2500 installed in the United Kingdom for the production of tunnel coverings;
• 5 x BISON 500 between Hungary and Poland, for the production of road substrates;
• 1 x MMX 5000 installed in the United Kingdom for the construction of a wind farm;
• 2 x MMX 5000 and 1 x EAGLE 4000 which will be installed in Australia in these weeks for the Snowy 2.0 Hydroelectric Project;
Other important references, however, which see the supply of modular fixed systems of the WETBETON line, designed for massive production of concrete at work:
• The Great Dam of Ethiopia, Renaissance DAM;
• Follow Line Norway, railway tunnel;
• Extension of the Panama Canal;
• Neckertal Dam, Namibia;
• Changuinola Dam, Panama;
• Hong Kong Airport, China;
• Nam Theun Dam, Laos;
• Project of the Meuse, Italy
Mobile concrete plants: what matters most
4. Is installation speed really important for a mobile system? Or does its hourly production capacity matter more?
Federico Furlani:
Of course there are several applications in which different characteristics are given priority. In general, the philosophy with which SIMEM designs the plants starts from the guarantee of concrete quality, regardless of mobility or production capacity. Over the years we have been able to develop solutions that minimize the costs and times of transport and assembly of plants with the aim of allowing our customers to intervene on projects of even small scale, without compromising the profitability of their order. As for production capacity, the range we offer covers the widest possible range, from 10 to 1000 cubic meters now, for the needs of the small residential construction site rather than the large hydroelectric project.
Which concrete mixer is mounted
5. What pre-drainer mounted in general, type and brand ?
Federico Furlani:
The heart of the SIMEM system is the mixer, which has always been produced in our factories.
There are these macro categories:
• Planetary mixers, XENTRIX range, generally used in the precast industry;
• Double-axis batch mixers, RHYNO range, for the ready-mix industry and large projects;
• Continuous dual-axis mixers, MDC range, generally for inertization, cemented mixed, and mining industry
What automation and moisture probes are installed
6. Do you mount your own automations or do you have an external partnership?
Federico Furlani:
Depending on the type of plants and their destination we use software both from third parties and developed in the SIMEM automation department.
The logic of the process and the overall management of the plants always remains within the competence of SIMEM that guarantees customers all the support and assistance necessary for the entire life of the plants that, in some cases, exceeds several decades.
We have also developed a digital platform for remote support and on this we are processing data management functions to optimize the concrete production process.
7. What kind of moisture probes of aggregates is your plant typically made with?
Federico Furlani:
The measurement of the humidity of the aggregates, with the use of the latest generation micro-wave probes, is implemented in the operating system of the plant, which automatically recalculates the amount of water to be dosed in accordance with the mix – design selected by the operator.
8. Are your carpentry treated to withstand corrosion? If you how?
Federico Furlani:
The carpentry of SIMEM plants is treated to prevent corrosion phenomena through the hot galvanizing process. Unlike painting treatments, hot galvanizing offers deeper protection that ensures a long life for our facilities for any weather conditions. All SIMEM systems are then made with bolted modular elements that allow to assemble customized solutions as well as allow the replacement of damaged elements quickly and cost-effectively, extending the useful life of the plants much longer than most plants that to date are produced with welded structures.
After-sales service
9. Do you give direct after-sales assistance, or do you rely on an external partner?
Federico Furlani:
The Service & Spare Parts department is dedicated to all after-sales operations, giving support to all our customers in Italy for any type of need.
The help-desk service, with remote control, allows our technicians to connect for system diagnoses, and to help solve possible problems on site.
As for the rest of the world, SIMEM has established its own production, commercial and service subsidiaries in America, Canada, India and Russia, while in other countries it has entrusted the distribution and assistance of its plants to local partners representing quality machines such as Caterpillar or Wirtgen
How and why to choose a mobile system
10. Through what concrete assessments can a contractor assess the quality of a mobile plant being purchased?
Federico Furlani:
According to SIMEM, the quality of the concrete produced cannot be compromised when choosing a mobile plant, which must therefore guarantee the same standards (if not better) as a fixed concrete plant.
There are also very mobile proposals on the market which, however, adopt insensil dosing systems and questionable mixing methods, unless they are interventions that do not qualify as concrete. An additional value of our mobile system, which gives concrete results already when the implant is switched on, is the dosing accuracy of the binders, with a dosing error below 2%. By avoiding unnecessary waste, the customer can save on the consumption of the most expensive material required in the mixing process
Guaranteed quality, the other important characteristics to pay attention to are the ease of transport and installation, the solidity of the structures and set-up mechanisms that allow to withstand multiple movements, the flexibility to produce a wide range of concretes to be applicable in the most diverse situations, the maintenance of the value of the investment over time to maximize the residual value of the asset in case you want to resell.
11. Discontinuous or continuous pre-mixing: what is the best solution for a mobile system?
Federico Furlani:
Continuous plants are traditionally designed for the production of cemented mixtures, RCC, road substrates where the large production capacity required (typically between 100 and 500 tons/hour) does not require too much dosing precision.
Discontinuous plants, on the other hand, for the same investment, favor dosing accuracy and the determination of mixing times that vary according to the mix design, sacrificing production capacity over continuous.
These categories are, however, close to the range of SIMEM plants since the evolution of our innovations today allow to combine the great production capacity of the continuouss with an extreme precision of dosages, so that with the BISON range you can package in continuous concrete, such as draining, with the maximum accuracy of the weighing of aggregates, binders and additives, while maintaining production capacities equivalent to those of discontinuous plants.
On the other hand, the discontinuous and supermobile MMX system allows to produce, always with maximum precision, concretes of any type up to 130 cubic meters / hour, how much and more than a typical fixed concrete plant!
12. Why would a traditional concrete manufacturer need a mobile plant?
Federico Furlani:
The Italian market of the last 12 years, from 2008 onwards, has fought its “Third World War” with a contraction in volumes that has forced all producers to make great efficiency. It has become impossible to make more extensive forecasts than a few quarters and the geography of demand is exposed to continuous changes of course. In a situation like this the watchword becomes flexibility and therefore it is unthinkable to plan the purchase of a fixed power plant that in normal times had an average life of 20-30 years and on that term the valuations of the investment were aligned.
Today the added value that a concrete manufacturer can exploit to successfully manage its business is technological know-how (knowing how to do concrete well) and the flexibility of service to customer companies. Integrating its production structure with some mobile system therefore becomes a strategic lever to apply to provide concrete especially in the infrastructure works that we hope the recovery plan can take off.
13. When a mobile system is preferable to a fixed plant: what factors should be taken into account in the cost/benefit assessment?
Federico Furlani:
By reaffirming the lowest common denominator of quality that must be guaranteed, logistics becomes a fundamental element of evaluation. Depending on the location of the construction site where the concrete is requested, the criteria of “lean production” can determine the choice of the plant and the means necessary to feed it and to distribute the concrete in operation. Obviously there are plants and plants and therefore the reliability of the dosing and mixing process, the speed of transport and assembly, the production capacity and the value (which means not only the price but the purchasing equation, management cost and residual value at the end of the work) can determine different evaluations.
Our mobile systems, for example, do not require civil works for positioning, which result in significant economic savings, as well as a possible by-pass of the authorizations required for fixed plants.
Certainly, from a logistical point of view, a mobile system makes a difference in road or rail works, where the production plant can be moved several times to follow the axis of progress of the construction site area.
14. Do you provide mobile rental facilities? If so, even with the rental with staff ?
Federico Furlani:
We give the possibility to rent our plants, taking care of transport, installation and testing on site.
Our specialized technicians make sure to complete the training with the customer’s operators, who will then manage the production for the agreed period.
15. Do you guarantee a buyback price at the end of the construction site?
Federico Furlani:
SIMEM proposes a BUY-BACK, calibrated on the duration of the construction site and the expected production of the plant. Typically the market value of SIMEM plants is recognized as premium and therefore guarantees good resaleability both in Italy and abroad where, in the last 20 years, our company has achieved up to 90% of its turnover.
16. In conclusion, why choose your own plant?
Federico Furlani:
SIMEM’s mission is not so much to sell plants, but rather to generate value for the business of concrete manufacturers by advising, creating, providing and assisting solutions that link our company to those of our customers for the life span of the machines. Those who choose to buy the most important element of their production process from a supplier must choose the technology but also the company that develops and realizes the technology.
For this reason we believe that today SIMEM represents one of the best candidates in the world to guarantee those who produce concrete reliable solutions in terms of quality and service, innovative, efficient and competitive, gained thanks to international experience in over 57 years of activity.
We have among our references the largest works built all over the world and we look forward to contributing to the construction of new great works also in Italy, assisting the very good concrete producers of our country.
The mission has always been to develop innovative solutions for the production of concrete, which today are declined in the widest range of plants and machinery for the most diverse applications: from pre-packaged concrete to prefabrication, from road pavements to the construction of tunnels and mines, from the construction of dams and megaprojects to the treatment and inertization of contaminated soils.
SIMEM operates worldwide through a number of subsidiaries and manufacturing facilities in America, Canada, Russia and India, serving all other markets through dealers and partners that distribute leading industry brands such as Wirtgen and Caterpillar
In recent years the Group’s technologies have expanded to the world of automation for prefabrication with the integration of Schiaslo Spil of Treviso and in the field of tunneling and mining with the acquisition of Team Mixing of Vancouver BC.
Solutions for perfect concrete is the motto with which SIMEM offers added value to its selected customers